Oil Seal Manufacturing: Ensuring Quality in Diesel Engine Parts
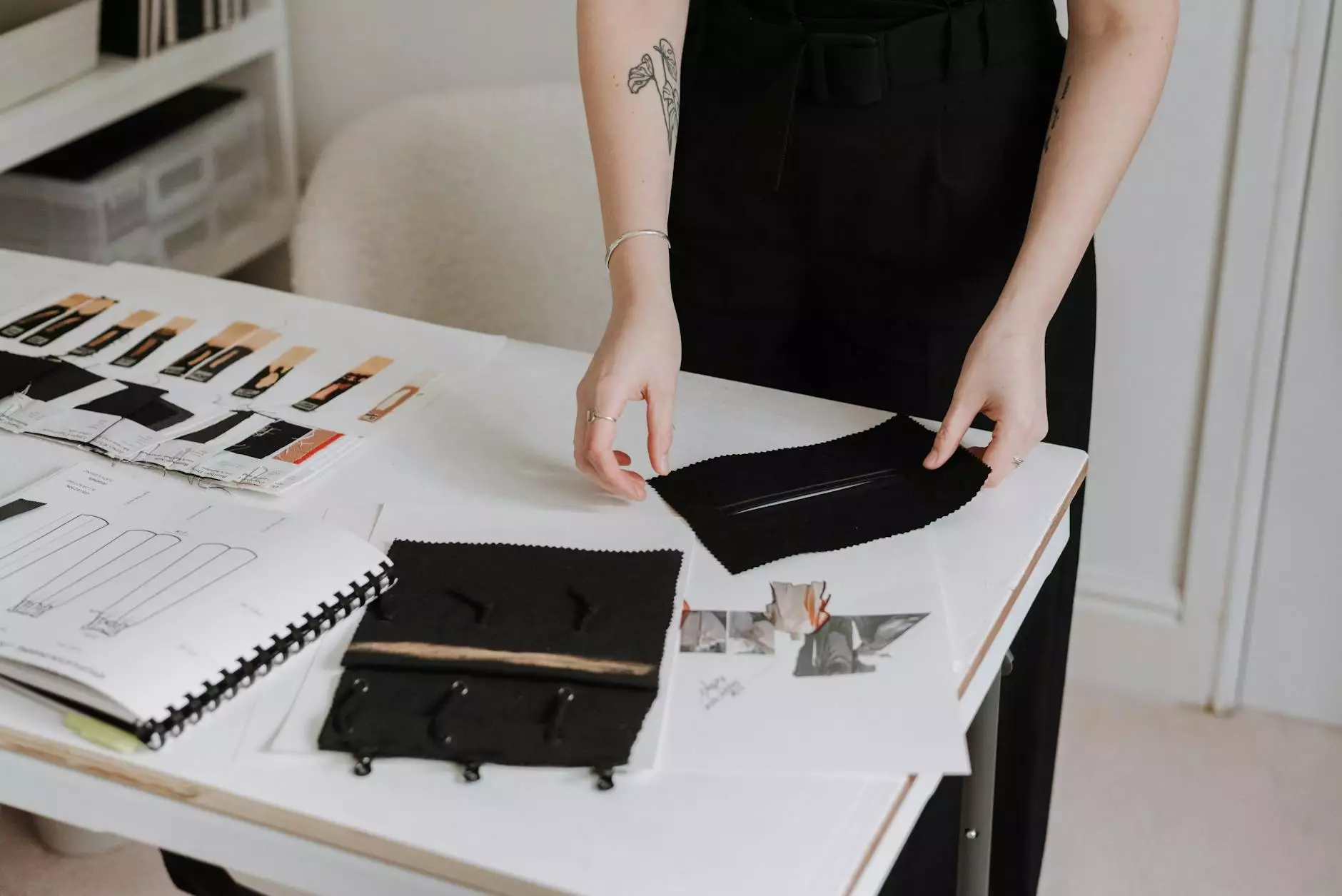
In the intricate world of diesel engine parts, the importance of reliable components cannot be overstated. One such critical component is the oil seal, which plays a vital role in maintaining the integrity and efficiency of diesel engines. This article dives deep into the realm of oil seal manufacturing, shedding light on its significance and the processes involved in creating top-notch products that meet industry standards.
Understanding Oil Seals
Oil seals, also known as fluid seals, are designed to retain lubricant and exclude contaminants from entering engine components. They are essential in ensuring that oil remains contained, preventing leaks that can lead to engine failure. The efficiency and longevity of a diesel engine largely depend on the quality of these seals. Here’s why they are critical:
- Leak Prevention: Oil seals prevent the escape of fluids, ensuring that the engine operates smoothly.
- Contamination Protection: They protect the engine from dust, dirt, and other contaminants that could cause wear and tear.
- Temperature Regulation: High-quality seals help maintain optimal temperature within the engine by ensuring proper lubrication.
Types of Oil Seals Used in Diesel Engines
When it comes to oil seal manufacturing, there are various types of oil seals employed in diesel engines, each tailored for specific applications:
1. Radial Oil Seals
These seals are designed to fit between rotating shafts and stationary housing. They are common in various engine applications, effectively preventing oil leakage while also excluding dirt.
2. Axial Oil Seals
Axial seals, which work along the axis of the shaft, are used to seal the ends of cylindrical shafts. They are less common but critical in certain engine designs.
3. Lip Seals
Lip seals feature a flexible elastomer lip that creates a dynamic seal against the shaft. They are widely used in automotive applications due to their effectiveness in low-friction scenarios.
The Oil Seal Manufacturing Process
The process of oil seal manufacturing involves several critical stages, each ensuring that the final product meets the required specifications.
1. Material Selection
The first step in manufacturing oil seals is selecting the right materials. Commonly used materials include:
- Rubber: Commonly used for its elasticity and resistance to oils.
- Polyurethane: Known for its durability and wear resistance.
- Vinyl: Often used for softer seals that require flexibility.
2. Molding Techniques
Oil seals are typically created using molding techniques such as:
- Compression Molding: Involves placing raw material in a mold where heat and pressure shape it.
- Injection Molding: Material is injected into a mold cavity, allowing for precise and complex shapes.
- Transfer Molding: A hybrid of compression and injection molding, suitable for larger seals.
3. Quality Control
Quality control is paramount in oil seal manufacturing. Manufacturers employ various testing methods, including:
- Pressure Testing: Ensuring seals can withstand pressure without failure.
- Temperature Testing: Evaluating seals under extreme temperatures.
- Flexibility Tests: Assessing the elasticity and flexibility of the seals.
Why Quality Matters in Oil Seals
Investing in high-quality oil seals is essential for several reasons:
- Enhanced Engine Performance: Quality seals ensure optimal lubrication, leading to better engine performance.
- Extended Longevity: Durable seals reduce the risk of leaks and engine damage, prolonging engine life.
- Cost Efficiency: While premium products may involve a higher upfront cost, they ultimately save money in repairs and replacements.
Oil Seal Suppliers: Finding the Right Partner
When procuring oil seals, partnering with reputable suppliers is essential. Companies like Client Diesel specialize in providing high-quality diesel engine parts, including oil seals that meet international standards. Here are some tips for choosing the right supplier:
- Experience: Look for manufacturers with a proven track record in oil seal manufacturing.
- Certifications: Ensure they comply with industry certifications, indicating quality assurance.
- Customer Reviews: Research feedback from previous clients to gauge reliability.
- Warranty Offers: Opt for suppliers that provide warranties on their products, ensuring confidence in quality.
The Future of Oil Seal Manufacturing
As technology progresses, the oil seal manufacturing industry is evolving. Innovations such as:
- Advanced Materials: New rubber compounds and synthetic materials are being developed for better performance.
- Automation: Increased automation in manufacturing processes enhances precision and efficiency.
- Sustainability: Manufacturers are focusing on eco-friendly practices and materials, appealing to environmentally conscious consumers.
The drive for innovation ensures that the industry adapts to changing demands and continues to provide products that meet the emerging needs of the automotive sector.
Conclusion
In conclusion, oil seal manufacturing is a cornerstone of the diesel engine parts industry, playing a crucial role in ensuring the reliability and efficiency of engines. Understanding the processes, types, and significance of oil seals can empower consumers and manufacturers alike to make informed decisions. By investing in quality products from trusted suppliers such as Client Diesel, you can guarantee the longevity and performance of your diesel engine.
As the industry continues to evolve, staying abreast of the latest advancements in materials and manufacturing techniques will be vital for maintaining a competitive edge. By prioritizing quality and reliability, we can look forward to a future where diesel engines operate smoothly and efficiently, powered by top-tier oil seals.