Machine Parts Precision CNC: Revolutionizing Metal Fabrication
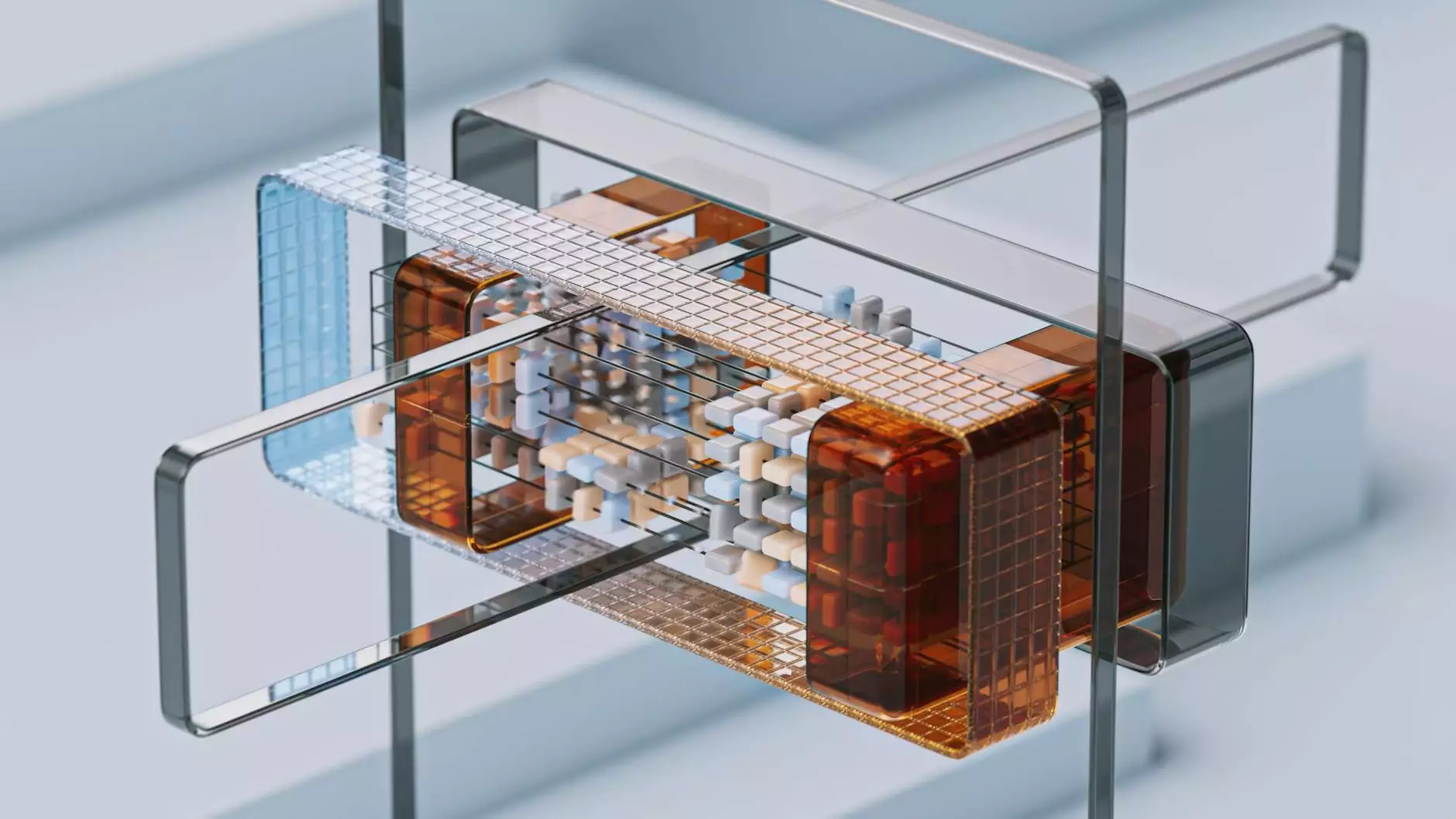
In today's rapidly evolving manufacturing landscape, the demand for precision and efficiency has reached an all-time high. The advent of machine parts precision CNC technology has fundamentally changed how metal fabricators operate, allowing for unparalleled accuracy and reduced wastage. In this article, we will explore the transformative impact of CNC machining on the metal fabrication industry, its benefits, applications, and why choosing a skilled provider is crucial for your business success.
Understanding Machine Parts Precision CNC
The term CNC stands for Computer Numerical Control, which refers to the automated control of machining tools (such as drills, lathes, and mills) by means of a computer. This technology allows engineers and machinists to produce parts with intricate designs and tight tolerances, making it an ideal choice for industries that require high-precision components.
How CNC Works
CNC machining involves several key steps:
- Design: The first step is creating a digital model of the part using CAD (Computer-Aided Design) software.
- Programming: The CAD model is then converted into a CNC program, which contains all the instructions for the machine.
- Machining: The CNC machine follows the programmed instructions, controlling the movement of tools to cut and shape the material.
- Finishing: Finally, the part may undergo additional processes like sanding or coating to achieve the desired finish.
Benefits of Machine Parts Precision CNC
Utilizing machine parts precision CNC offers numerous advantages that can significantly enhance manufacturing processes. Here are some of the most notable benefits:
1. Unmatched Precision
One of the most significant benefits of CNC machining is its ability to produce parts with high precision. Traditional machining methods often involve manual adjustments, which can lead to errors and inconsistencies. In contrast, CNC machines operate on a programmed path, ensuring each part is produced to the exact specifications required.
2. Improved Efficiency
CNC machines can operate continuously throughout the day, without the consistent oversight that manual machining requires. This leads to reduced production times and increased output, enabling businesses to meet customer demands more effectively.
3. Versatility in Production
From manufacturing simple components to complex designs, machine parts precision CNC can handle various materials, including metals, plastics, and composites. This versatility allows metal fabricators to diversify their offerings and cater to different industry needs.
4. Cost-effectiveness
While the initial investment in CNC technology can be significant, the long-term savings are substantial. The reduction in material waste, decreased labor costs, and improved production rates contribute to a lower overall cost of production.
Applications of Machine Parts Precision CNC
The applications of machine parts precision CNC are vast, touching almost every industry that requires high-quality manufacturing. Some common applications include:
- Aerospace Components: CNC machining is critical in producing parts that must adhere to strict safety and reliability standards.
- Automotive Manufacturing: Precision CNC is widely used to manufacture engine components, frames, and other critical parts.
- Medical Devices: The medical industry relies on CNC machining for producing surgical instruments, implants, and other precise components.
- Electronics: CNC is used for creating housings, connectors, and various electronic enclosures that require high precision.
- Industrial Equipment: Precision parts for machinery and tools are manufactured using CNC techniques.
Why Choose a Skilled CNC Provider
To fully leverage the advantages of machine parts precision CNC, it is essential to partner with a skilled provider that understands your specific needs. DeepMould.net specializes in metal fabrication and is equipped with state-of-the-art CNC technology. Here are several reasons why selecting an experienced CNC provider like DeepMould is beneficial:
1. Expertise in Design and Engineering
With specialized knowledge in both CNC machining and metal fabrication, a skilled provider can assist in optimizing designs for manufacturability, ensuring that every part produced meets the highest standards of quality.
2. Access to Advanced Technology
The latest CNC machines are constantly evolving, providing improved efficiency and capabilities. A proficient provider invests in the latest technologies, enabling them to produce complex parts that may be out of reach for less equipped companies.
3. Commitment to Quality Control
Quality assurance is paramount in CNC machining. A reliable provider implements thorough inspection processes at each stage of production to ensure that all parts meet required specifications. This attention to detail reduces the risk of defects and customer dissatisfaction.
4. Custom Solutions
No two projects are alike, and having a partner that can tailor solutions specifically to your needs is invaluable. DeepMould works closely with clients to understand their objectives and develops custom CNC solutions that align with their manufacturing goals.
Challenges and Considerations in CNC Machining
While the benefits of machine parts precision CNC are clear, there are also some challenges involved. Understanding these factors can help businesses better navigate the CNC machining landscape:
1. Initial Investment
The cost of purchasing and maintaining CNC machines can be a barrier for some businesses. However, it is important to view this as a long-term investment that will pay off in increased productivity and reduced waste.
2. Skilled Workforce Requirement
Operating CNC machinery requires a skilled workforce proficient in programming and machine operation. Companies must invest in training and education to develop the necessary skills among employees.
3. Maintenance and Downtime
CNC machines require regular maintenance to ensure they operate efficiently. Downtime due to machine failure can negatively impact production schedules. Partnering with a provider that offers support and maintenance can mitigate this risk.
The Future of CNC Machining in Metal Fabrication
The future of machine parts precision CNC looks promising, with advancements in technology continuing to drive the industry forward. Some trends to watch include:
- Automation: The integration of robotics and automation in CNC machinery will enhance productivity and reduce labor costs.
- AI and Machine Learning: These technologies are being used to optimize machining processes and predict maintenance needs.
- Eco-Friendly Practices: Sustainable practices in CNC machining, such as using recycled materials, will gain traction as industries focus on reducing their environmental impact.
- Additive Manufacturing: The intersection of CNC machining and 3D printing is creating new possibilities for complex parts and reduced lead times.
Conclusion
In conclusion, machine parts precision CNC has fundamentally transformed the metal fabrication landscape, offering numerous advantages such as unmatched precision, improved efficiency, and cost-effectiveness. By partnering with a skilled provider like DeepMould.net, businesses in various industries can harness the full potential of CNC technology. As the industry evolves, staying ahead of trends and investing in quality CNC services will be crucial for success in manufacturing.
For businesses looking to enhance their metal fabrication capabilities, understanding and implementing machine parts precision CNC technology will be the key to staying competitive in a fast-paced market.