The Comprehensive Guide to Concrete Mixing Plants
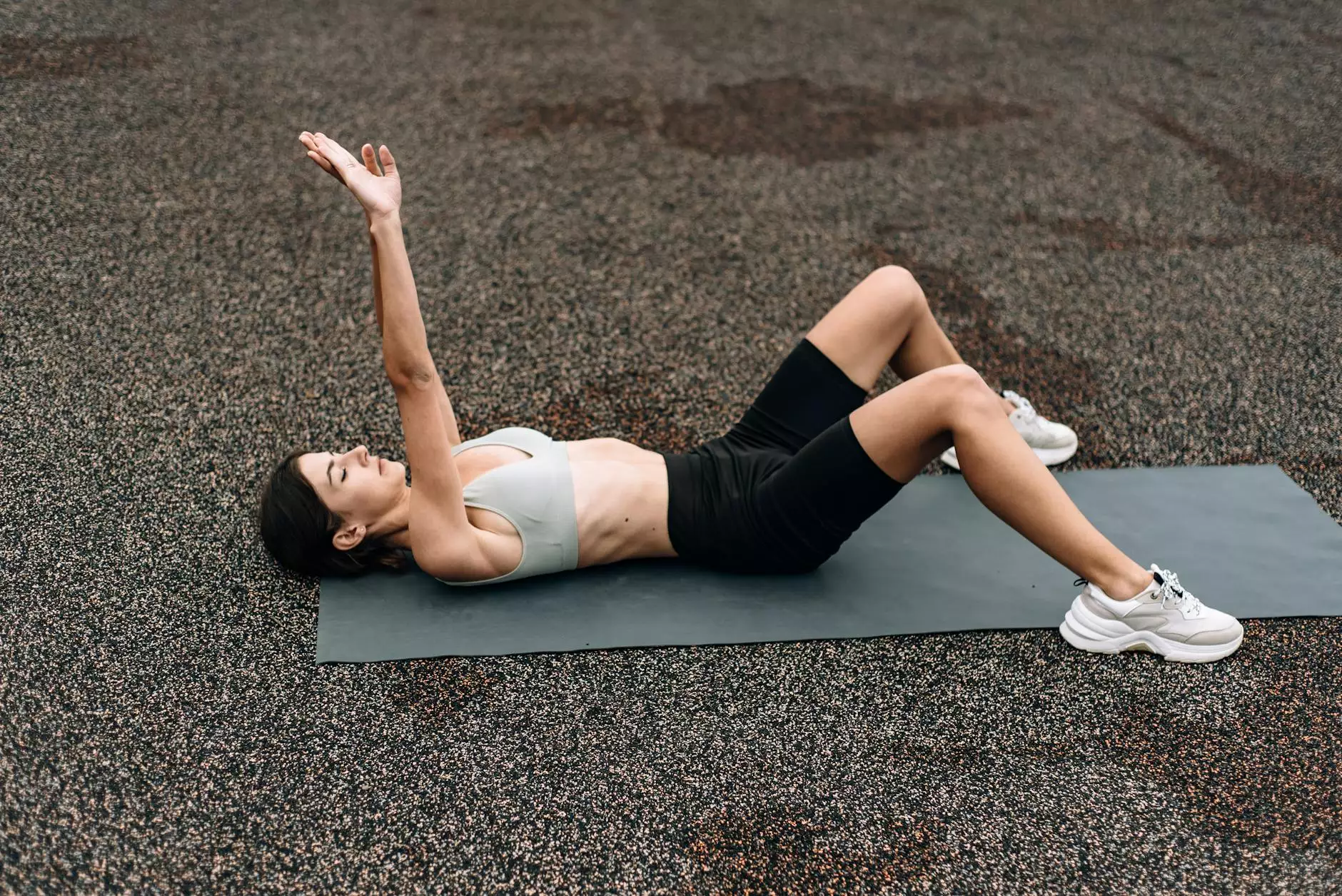
In the construction industry, the concrete mixing plant serves as a crucial component that significantly impacts the quality, efficiency, and cost-effectiveness of building projects. These plants are specifically designed to produce fresh concrete by combining various materials, including cement, aggregates, water, and additives. This article delves into the intricacies of concrete mixing plants, their types, functionalities, and the benefits they bring to the construction sector.
Understanding Concrete Mixing Plants
A concrete mixing plant is a facility that blends and mixes the ingredients required to create concrete for construction purposes. The process involves batching, mixing, and controlling the materials to deliver high-quality concrete that meets the specific needs of various construction projects. The seamless integration of modern technology in these plants has allowed for greater precision and efficiency.
Types of Concrete Mixing Plants
Concrete mixing plants can be categorized into various types based on their production capacity, design, and operational technology. Understanding these different types is vital for construction companies aiming to choose the right plant for their specific needs.
1. Stationary Concrete Mixing Plants
Stationary concrete mixing plants are designed to operate at a single location. These plants are ideal for large-scale construction projects due to their high production capacity and efficiency. The main features include:
- Fixed Production Capacity: Capable of producing several cubic meters of concrete per hour.
- Durable Design: Built using robust materials, ensuring longevity and reliability.
- Consistent Quality: Provides uniform mixing and consistent quality of concrete.
2. Mobile Concrete Mixing Plants
Mobile concrete mixing plants offer the advantage of flexibility and portability. These plants can be transported from one job site to another with ease. They are particularly beneficial for contractors operating in remote locations or for projects with varying site conditions. Key characteristics include:
- Ease of Transportation: Can be quickly assembled or disassembled.
- Versatile Use: Suitable for various small to medium-sized projects.
- On-Demand Production: Allows for concrete production on-site, reducing transportation costs.
3. Continuous Concrete Mixing Plants
These plants operate using a continuous flow of materials rather than batching them. This design is beneficial for projects that require a steady supply of concrete over an extended period. Important features include:
- High Efficiency: Reduces waiting time and increases productivity.
- Low Labor Requirement: Automated processes minimize the need for manual labor.
Components of a Concrete Mixing Plant
A concrete mixing plant consists of several key components that work together to ensure efficient production. Each component plays a unique role in the overall functionality of the plant:
- Aggregate Bins: Used to store different sizes of aggregates (sand, gravel, etc.) prior to mixing.
- Cement Silos: For storing cement, which is a pivotal ingredient in concrete production.
- Water & Additive Tanks: Tanks that hold water and any necessary additives that enhance the properties of the concrete.
- Control System: A sophisticated system for controlling the entire mixing operation, ensuring everything runs smoothly and efficiently.
- Concrete Mixer: The core component where all materials blend to produce the final concrete mix. This could be a drum mixer or a twin-shaft mixer, depending on the requirements.
The Importance of Concrete Quality
Concrete quality is vital in construction as it directly affects the integrity and durability of the structures built. The quality of concrete produced by a concrete mixing plant depends on various factors, including:
1. Material Selection
The choice of materials—cement, aggregates, water, and additives—plays a critical role in determining the strength and durability of the concrete. Higher quality raw materials result in superior concrete products.
2. Mixing Process
Proper mixing is essential to achieve uniformity in the concrete. Inadequate mixing can lead to inconsistencies, which may affect the structural integrity of the finished product.
3. Adherence to Standards
Following industry standards and regulations for concrete production is crucial. Many countries have established guidelines that dictate the acceptable ranges for various properties of concrete, ensuring safety and performance.
Benefits of Using a Concrete Mixing Plant
Utilizing a concrete mixing plant offers various advantages that support construction companies in achieving their project goals:
1. Increased Efficiency
Concrete mixing plants are designed for maximum efficiency. By automating the mixing process and reducing manual labor, construction teams can produce high volumes of concrete in shorter timeframes.
2. Cost-Effectiveness
By producing concrete on-site, companies can save on transportation costs and reduce waste. In addition, the ability to control the mixing process can help optimize material usage, leading to financial savings.
3. Customization
Concrete mixing plants allow for the customization of concrete mixtures to meet specific project requirements. This flexibility ensures that contractors can produce tailor-made concrete blends suited to different environmental conditions and structural demands.
4. Improved Quality Control
The use of modern technology in concrete mixing plants enhances quality control. Automated monitoring of ingredients and mixing times enables producers to maintain high-quality standards throughout the production process.
Choosing the Right Concrete Mixing Plant
Selecting the appropriate concrete mixing plant is critical for maximizing efficiency and meeting construction timelines. Here are several factors to consider:
- Project Size: Determine the scale of your project and the volume of concrete required.
- Site Conditions: Assess the logistics of the construction site, including accessibility for heavy equipment.
- Production Rate: Evaluate the desired production rate to choose a plant that meets your time requirements.
- Budget: Consider your budget for purchasing or renting the plant, as well as operational costs.
Future Trends in Concrete Mixing Plants
The construction industry is continuously evolving, and concrete mixing plants are no exception. Here are some emerging trends shaping the future of concrete production:
1. Innovative Technologies
Advancements in technology are leading to improved automation and monitoring systems in concrete mixing plants. By integrating IoT (Internet of Things) devices, operators can gain real-time insights into production processes, enhancing efficiency and quality.
2. Sustainability Initiatives
As environmental concerns grow, many companies are prioritizing sustainable practices. Future concrete mixing plants will likely incorporate eco-friendly materials and processes, reducing carbon footprints and promoting greener construction methods.
3. Modular Designs
Modular plants are becoming increasingly popular due to their ease of transport and quick setup times. This trend allows for more flexibility and rapid deployment on various job sites.
Conclusion
In conclusion, a concrete mixing plant is an indispensable asset in modern construction. Understanding the various types, components, and benefits of these plants not only allows for a better selection process but also enhances overall project success. As the industry continues to innovate, embracing new technologies and sustainable practices will further improve the role of concrete mixing plants in shaping the future of construction.
For more information on concrete solutions and the latest technology in the construction industry, visit polygonmach.com.